Besuch der Epiroc Deutschland GmbH
Am dritten Tag unserer Exkursion waren verschiedene Besuche geplant: Der Tag sollte mit einer Werksbesichtigung bei der Epiroc Deutschland GmbH beginnen, danach waren wir bei der bergbehördlichen Aufsicht des Bundeslands Nordrhein-Westfalen eingeladen. Am Abend war ein Besuch der Drahtseilerei Bridon Bekaert geplant, die am Standort Drahtseile für den Bergbaueinsatz fertigt.
Der Tag begann mit der Anreise von unserer Unterkunft nach Essen. Dort hatten wir als AG Grubenwehr im Rahmen der ,,Ausfahrt West’’ die Möglichkeit einer Werksbesichtigung bei der Epiroc Deutschland GmbH. Epiroc Deutschland existiert in dieser Form erst seit diesem Jahr und geht direkt aus der Firma Atlas Copco hervor.
Wir wurden an dem Tag von Reiner Koch und Antje Matthäus empfangen, welche uns nach einer kurzen Einweisung durch Produktionshallen führten. Am Standort werden verschiedene Anbauwerkzeuge für bauliche und bergbauliche Tätigkeiten hergestellt. Ein besonderes Produkt sind dabei Hydraulikhämmer in der Gewichtsklasse von 750 bis 10.000 Kilogramm, die in der gesamten Welt zum Einsatz kommen.
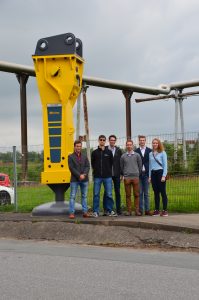
Die Produktion funktioniert logistisch betrachtet nach dem ziehenden System mit Meldung (Pull-Prinzip). Dabei wird über den gesamten Produktionsaufwand ein besonders hohes Augenmerk auf Sicherheit und Qualität gelegt. Die hochmodernen Maschinen erlauben eine Zerspanung auf bis zu 1/100 Genauigkeit. Von jedem einzelnen Produktionsschritt aus wird nur ,,Qualität weitergegeben’’, das heißt, dass nach jedem Arbeitsschritt der Mitarbeiter eine Werker-Selbstprüfung durchführt. Bei dieser Prüfung wird vermerkt, ob das Bauteil an dieser Stelle den Anforderungen entspricht und erst danach an den nächsten Fertigungsschritt weitergereicht. Eine zentrale Qualitätssicherung entfällt somit.
Alle Abläufe sind standardisiert; jeder Mitarbeiter kann dadurch auch in einer anderen Abteilung (einem sog. ,,Produktions-Schiff’) arbeiten. Um 8:30 Uhr stoppt jeden Morgen die Arbeit und der Teamleiter führt ein 15 minütiges Gespräch mit der Arbeitsgruppe. Es wird hierbei zwischen wöchentlichen und täglichen Informationen unterschieden. Täglich wird beispielsweise die Arbeitsleistung des Vortages ausgewertet und mit den Durchschnittswerten verglichen. Das soll dabei helfen, zum Beispiel durch Bewertung der Maschinenauslastungen Engpässe frühzeitig zu erkennen.
Die Ansprüche an die Qualität und das gewissenhafte Ausführen der eigenen Arbeit lassen sich genauso auf das Wirken innerhalb einer Grubenwehr oder speziell des Gerätewartes übertragen; ebenso wie die gegenseitige Absprache und Auswertung einer gegebenen Situation. An jedem Arbeitsplatz fiel das besonders hohe Maß an Ordnung und Sauberkeit auf. Gerade für die Arbeitsumgebungen, in denen prozessbedingt mit viel Abfall zu rechnen gewesen wäre, waren wir von der sehr gepflegten Erscheinung des gesamten Umfelds etwas überrascht. Dazu trägt bei, dass in regelmäßigen Abständen interne Audits, bei welchen die Mitarbeiter eines Schiffes eine andere Abteilung nach festgelegten Gesichtspunkten beurteilen, gehalten werden, um das Zurechtfinden und die sicherheitstechnische Unbedenklichkeit am Standort bestätigen zu können. Dabei hilft wohl vor Allem auch der etwas distanziertere Blick, um Verbesserungsvorschläge tätigen zu können. Aber auch zum Kennenlernen der anderen Arbeitsplätze trägt diese Systematik bei. Am Produktionsstandort in Essen wird in einem 3-Schichtsystem gearbeitet, ab November ist es aufgrund der großen Nachfrage geplant auf ein 4-Schichtsystem zu wechseln.
Eine Besonderheit der Hydraulikhämmer ist das automatische Einstellsystem AutoControl: bei jedem Schlag kann im Hammer ermittelt werden ob das im Angriff stehende Material eher hohe oder eher niedrige Festigkeit besitzt. Danach können die Frequenz und der Hub individuell angepasst werden. Jeder Hydraulikhammer wird nach der Endmontage auf Funktion auf einer speziellen Testapparatur überprüft. Bei der Leistungskontrolle werden im speziellen Umfeld Schläge auf ein Opfermaterial ausgeführt. Dieses gibt die Energie über einen angeschlossenen Stahlplattenverbund weiter, in dem die Kräfte abgebaut werden.
Um der extrem hohen, schlagenden Belastung standhalten zu können werden einige Bauteile plasmanitriert. Das Bauteil wird dazu in einem speziellen Ofen montiert und von Stickstoff umströmt. Der Ofen stellt bei dem Prozess die Anode, und das Bauteil die Katode dar. Es entsteht bei dem Prozess das namensgeben Plasma welches dem Stickstoff ermöglicht in das Material hinein zu diffundieren.
Im Anschluss zu der Führung konnten noch einige Fachfragen im Gespräch geklärt werden. Eine tiefergehende Absprache auf dem Gebiet einer Zusammenarbeit auf dem Gebiet der Rettungswerke zwischen der Epiroc Deutschland GmbH und der AG war uns leider nicht möglich. Wir bedanken uns sehr herzlich für die Führung, das Beantworten all unserer Fragen und die uns gewidmete Zeit! Die Eindrücke, die sich im Rahmen der Befahrung der Werkshallen ergeben haben, können wir in einigen Punkten auch auf die Arbeit unserer Arbeitsgemeinschaft übertragen und wir hoffen auf ein in Zukunft weiterhin gutes Klima und unkomplizierte Absprachen.
(Wir hoffen auf Verständnis, das Fotografie innerhalb des Werkes nicht gestattet war)